Major Hazard facilities and regulations
In 2015, the Health and Safety at Work Act was introduced, and with it, the introduction of new regulations for Major hazard facilities (MHF). These new regulations provided a framework for additional health and safety requirements that must be met and complied with by business’s that have hazardous substances over a set threshold. These regulations are overseen and monitored by a specialist team within WorkSafe known as the WorkSafe high hazard unit. This additional oversight provides assurance to the community that MHF sites have undertaken comprehensive safety assessments and are managing all hazards and risks that they may pose to their workers and the community.
Arch Wood Protection (Trading as Arxada wood protection)
The Auckland Arch wood protection site is located at 265 James Fletcher Drive, Otahuhu, Auckland and is categorised as an upper tier Major Hazard Facility under the New Zealand Health and Safety at Work (Major Hazard Facilities) Regulations 2016.
Manufacturing and supplying a portfolio of trusted wood protection products including industry leading brands such as Tanalised, Tanalith, Vacsol and Antiblu, Arch wood protection works in partnership with wood processors throughout the Asia pacific region to preserve, protect and enhance the durability and resilience of wood products against decay, mould, termites, fire and other hazards. Timber preservation products essential in the treatment and protection of wood products have been manufactured at the Otahuhu site for over 30 years (under several different business names). Manufacturing is undertaken using relatively mild batch manufacturing methods. There are no temperatures that exceed 100c and all mixers and tanks operate under atmospheric conditions.
Arch have always strived to identify all hazards associated with the operation of the plants, and to put in place controls to mitigate these risks. We manage the risks associated with our operations through the implementation of our risk management system, which is integral to our comprehensive safety management system. We continually strive to improve our systems and safety performance. Our approach to safety and corporate citizenship extends beyond strict compliance with applicable laws.
Our Values:
Safety and Health – Committing to safety and health is a top priority for all of us. This encompasses our employees, our contractors, our customers, and the people in the communities where we do business.
Ethical Behaviour – We behave as respected corporate citizens, in accordance with the highest ethical standards and in compliance with all applicable regulations and laws.
Respect for People and planet – We treat all people with professionalism, dignity, and respect, fostering an environment of collaboration, innovation, excellence, and inclusion. We provide science-led solutions for our customers helping them to adapt to long-term environmental and social change and develop more sustainable solutions while we actively reduce our environmental footprint.
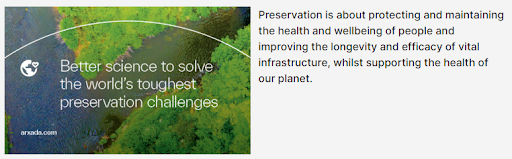
Safety Case
A requirement for upper tier major hazard facilities to operate, is to have a safety case accepted by WorkSafe. The safety case for Arch wood protection was accepted by WorkSafe New Zealand on 31 July 2020. The safety case demonstrates the safety management system, systematic safety assessments and emergency response planning that are used to operate the site and its hazards safely. The safety case demonstrates how the plant is being managed and operated safely to ensure that risks to personnel, damage to property and risk to community is reduced to so far as practical levels. Extensive engagement with key stakeholders, workers and the community is undertaken as part of safety case preparation and review. In particular, the safety case illustrates how the major incident hazards at the site are identified, understood and controlled. It also facilitates further continuous improvement in our safety and reliability performance and provides a mechanism to demonstrate compliance with the regulations.
Identification of controls and safety critical elements used on site are an important component of managing hazards and potential risks. Control measures are clearly identified and documented with ongoing verification of suitability and effectiveness being undertaken regularly by qualified people.
Employees on site along with health and safety representation are actively involved in the development and implementation of operating and maintenance procedures, new projects and conducting risk assessments, audits and inspections. As part of the site’s commitment to continuous improvement, the safety case is reviewed and updated regularly.
Major incidents
A Major Incident is an uncontrolled event (i.e. escape, spillage, implosion, explosion or fire) at a major hazard facility, that involves specified hazardous substances and exposes multiple people to a serious risk to their health and safety (including risk of death) arising from an immediate or imminent exposure to hazardous substances as a result of the uncontrolled event or indirect effects of the uncontrolled event.
The site has the potential for a major incident to occur if in the extremely low event that an extensive fire was to occur within the site building that resulted in the boiling of specific bulk tanks of acutely toxic hazardous substances. The resulting smoke from the fire may pose a risk to the health of people within the local area. There are many well established controls in place to prevent this risk from occurring.
Emergency management
Arch wood protection has consulted and worked closely with the local emergency services including the fire authority in the development of emergency response procedures for all major incidents that could potentially occur at the site.
The safety assessment has shown that the risk to the public is considered very low. Only a small number of events have the potential to extend off site. In the rare event that an emergency may occur on site, workers on site are trained to respond to the site emergency response plan. If emergency services assistance is required, the appropriate emergency service will be contacted immediately, and Fire and Emergency NZ (FENZ) will assume control of an onsite major incident. Site personnel with work and consult with FENZ, local authorities and other emergency service agencies as required.
Information to the local community will be provided by emergency communications (i.e. Emergency text alert system) if required, and may request people situated within the local area to shelter in place or to evacuate. If a shelter in place notification is received, please ensure doors and windows and closed and where possible air conditioning systems are turned off and await further updates as provided by emergency communications. If you experience any significant health effects or have difficulty breathing, please contact emergency services or health line immediately.
There is a low potential for incidents to disrupt traffic on James Fletcher Drive, however if this does occur, NZ Police will introduce traffic control points as appropriate.
If an emergency were to occur, after the emergency, additional information will be provided to the community and regularly updated by Arch when investigations are completed as required within the MHF regulations.
Safety management system
The established safety management system in place ensures that the safety assessment, safety case and associated requirements are maintained, reviewed, and revised to ensure ongoing continuous improvement in accordance with MHF regulations and good industry practice.
A key step of the safety case process is to involve employees and key stakeholders in completing a thorough safety assessment and ongoing reviews of the Otahuhu plant. The safety assessment identifies hazards that could potentially lead to a loss of containment (spill) and major incidents that could potentially occur if hazards are not effectively managed.
Each hazard identified is then assessed to determine the likelihood and consequences of a major incident occurring. Finally, we identify the controls already in place to prevent and mitigate a potential major incident and look at any additional controls that could be implemented or added to further reduce the risk to so far as is reasonably practicable.
Contact
We strive for operational excellence, and we are committed to engaging with the communities where we operate and helping them to understand our business. We believe it is fundamentally important to maintain open lines of communication with the community, and we have regular formal and informal communication with our neighbours, the local council, hospitals, and emergency services. We value these relationships, and the two-way communication channel created by this engagement, which helps us to continually improve the way we operate.
For further information please contact the NZ Manufacturing Manager Max Lauilhe on 06 755 9234
Further information regarding the requirements for major hazard facilities from the WorkSafe NZ website: https://www.worksafe.govt.nz/topic-and-industry/major-hazard-facilities/mhf-public-information/